

Production with the Highest Quality Standards
Fucine Film Solutions combines know-how, flexibility and reliability with 35 years of experience. We know the market and its requirements and work pro-actively to ensure that our customers have what they need, when they need it! Utilising only the finest raw materials, the films produced in Fucine are of outstanding quality. Every product must pass a series of low-tolerance quality checks. In addition, uniformity checks on colour and transparency of the PVC film as well as thickness control takes place during the calendaring & laminating process, ending with width control of the slitted, final reels. All final products are traceable back to the raw material.
We are ISO certified for Quality Management (ISO 9001) and Environmental Management (ISO 14001) and comply with the high BRC/IoP-standards. We are proud to have received the Class-A standard award regularly.
In short, the process includes:
-
Dosing and mixing: where the basic formulation is adjusted to suit the customer's needs. 95% of the raw material employed is fed, or weighed and mixed automatically.
-
Plastification of PVC mixture by extruders.
-
Calendaring: Processing of the extruded PVC mono-layer film as basis for further processing.
-
Processing of the PVC mono-layer film: either laminated with PE film (in line) or metallised with vaporised aluminium (off-line).
-
Winding: the PE laminated PVC film are wound onto rollers of up to 1000 mm. Metallised PVC is wound during the metallisation process • Slitting: although 90% of PVC/PE is slitted in-line, off-line slitting units are available (mainly for metallised PVC).
-
Packaging and despatch: packed rolls are stored in the finished product warehouse with truck docks for swift and efficient hand-over to logistic partners.
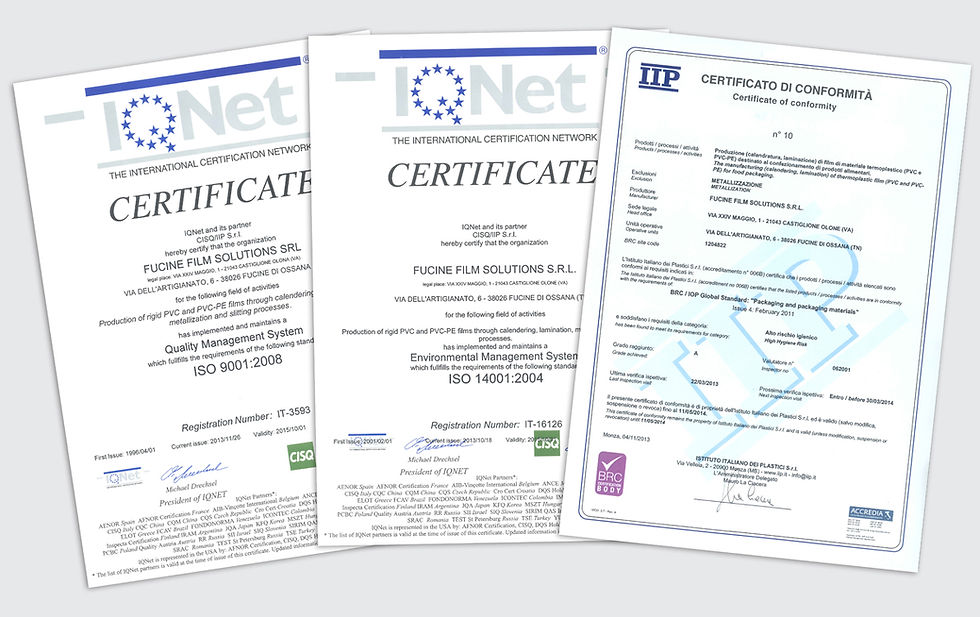

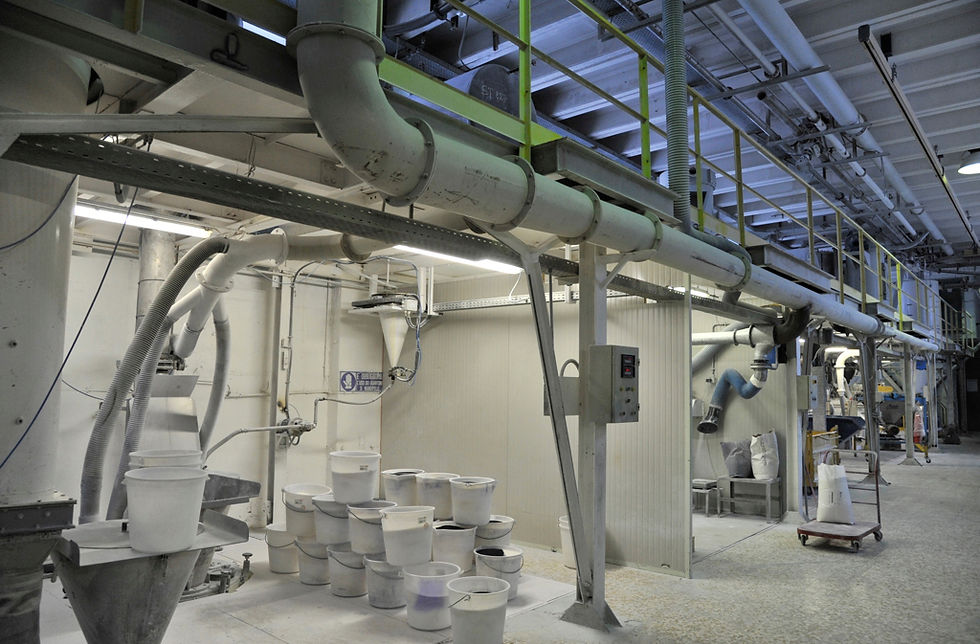
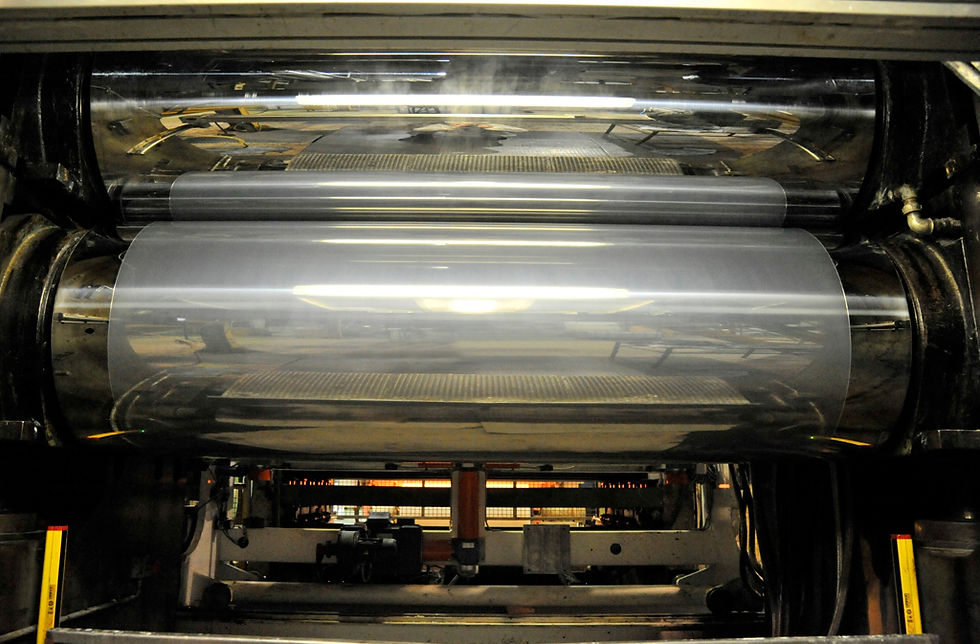
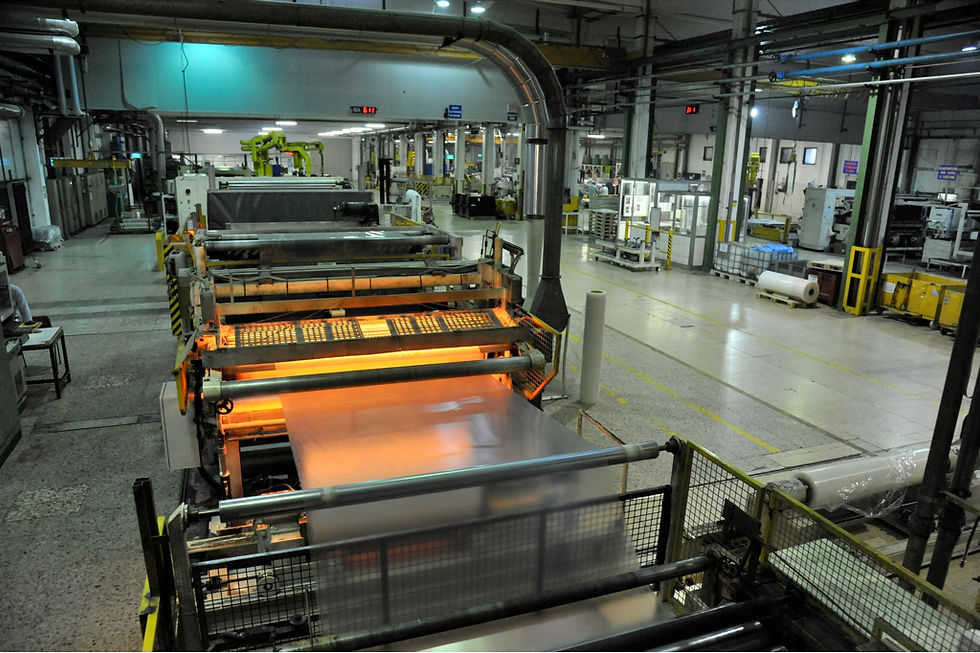
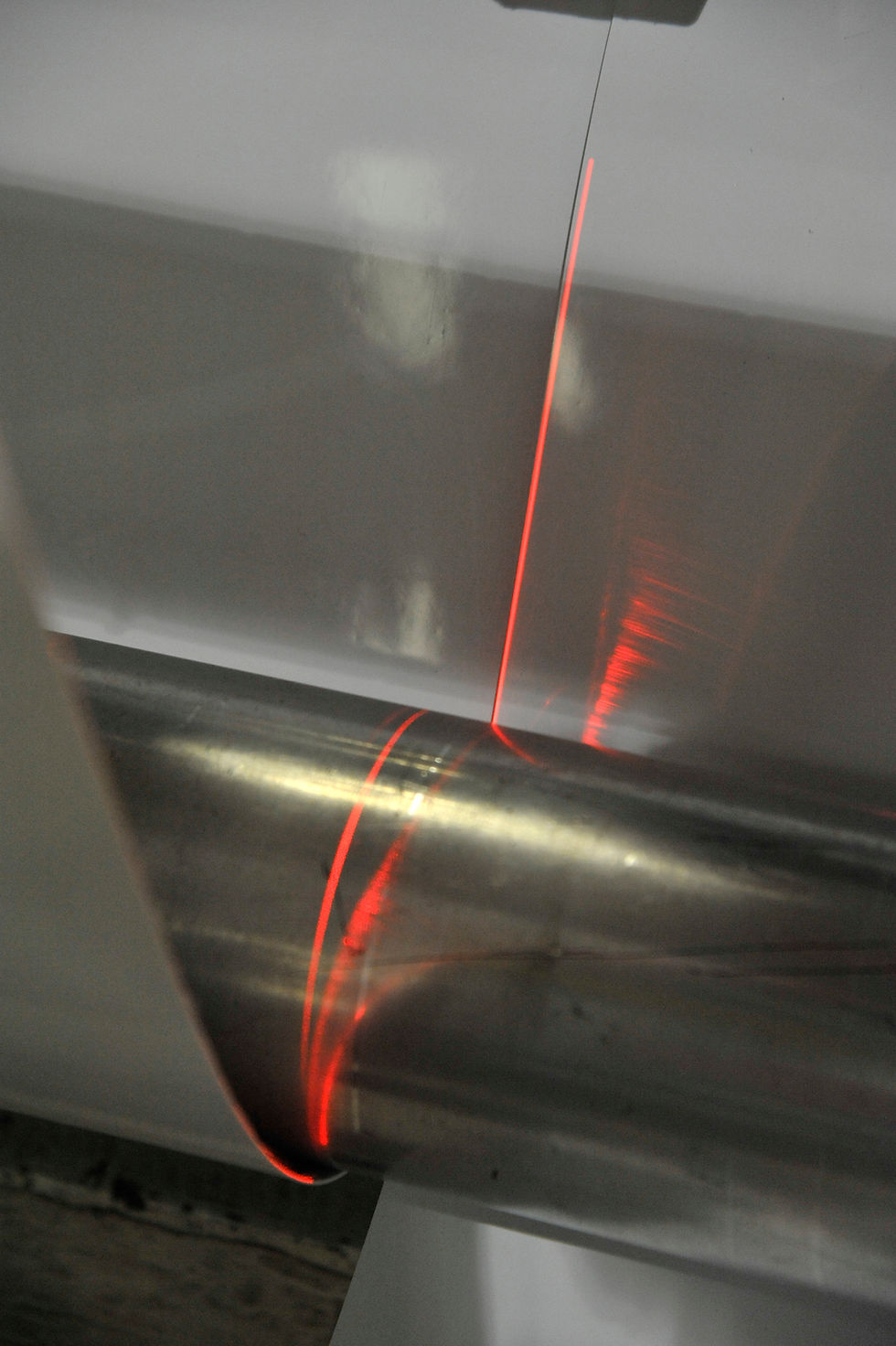

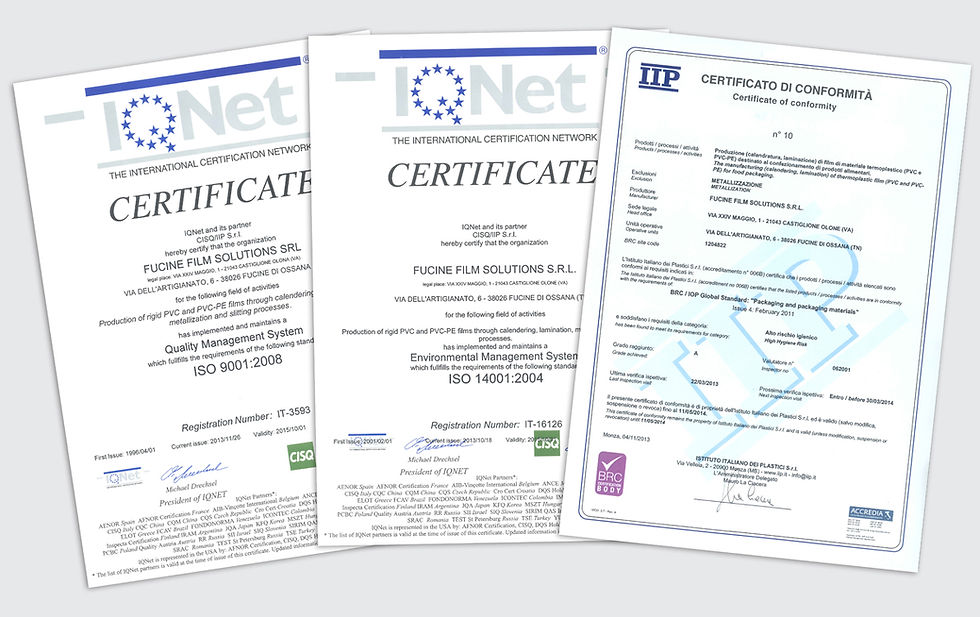

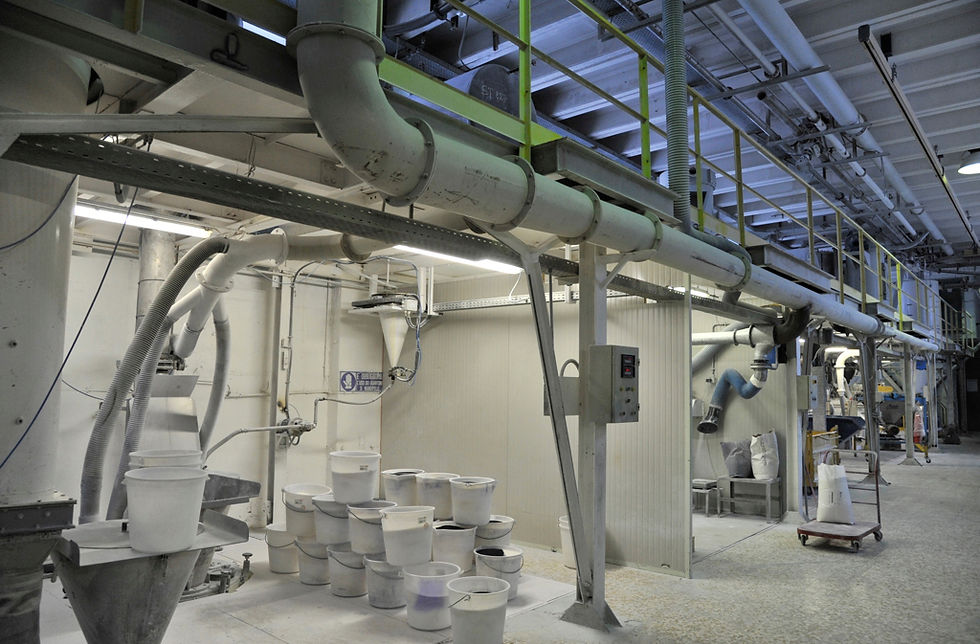
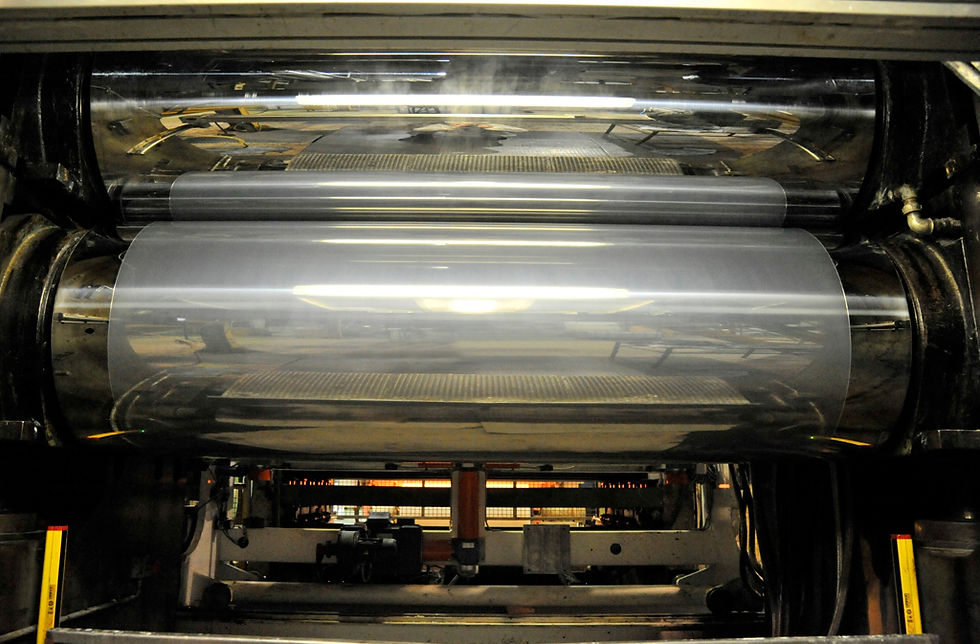
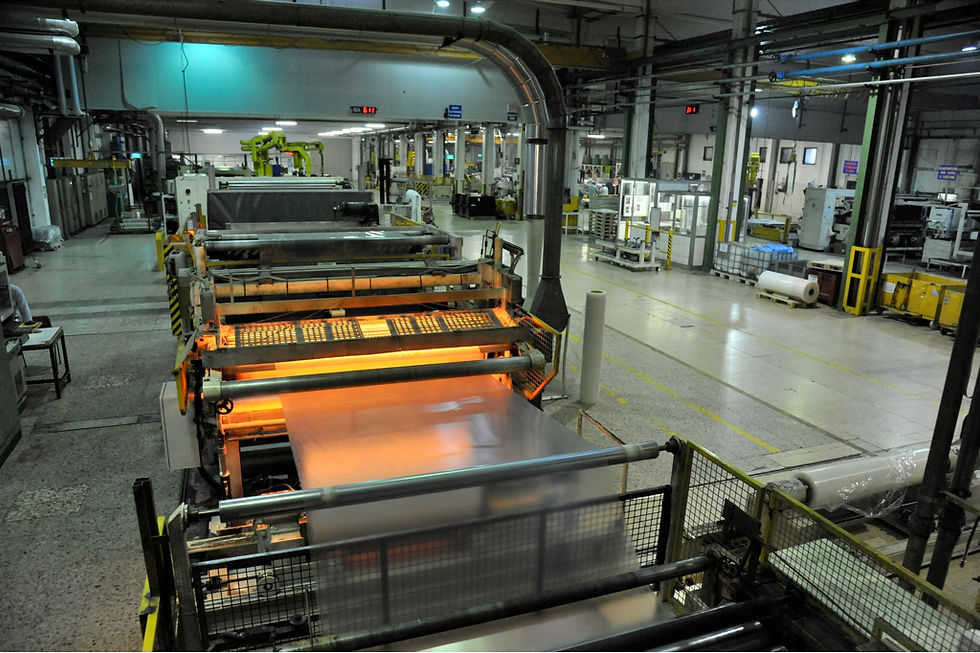
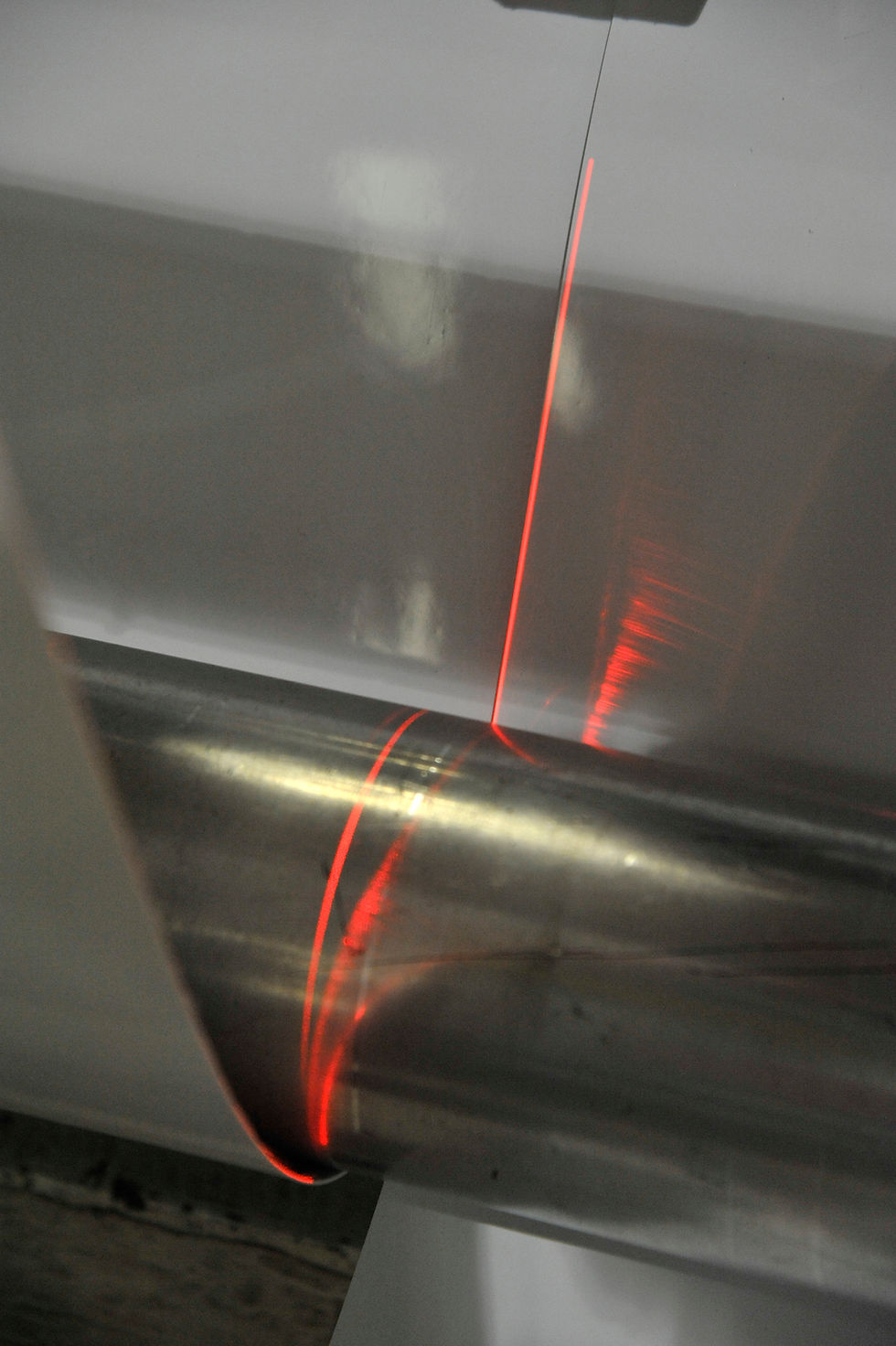
